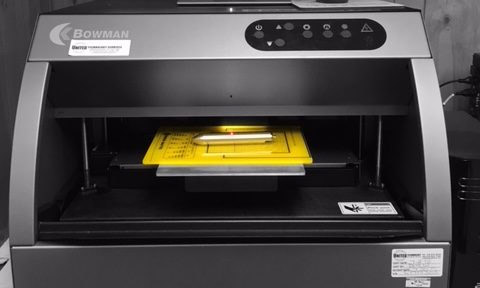

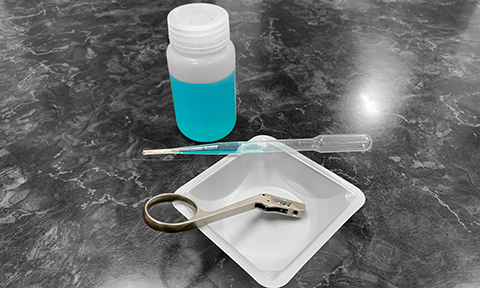
Quality Assurance
ECO understands the critical applications and demanding requirements of the markets we serve, and our processes are validated to meet those requirements and specifications. We provide metal finishing to many of the Top Medical Companies, Major Contract Manufacturers, Nuclear Energy Equipment Companies, as well as Cutting-Edge Start-Ups. Our focus is on providing quality, service, and value for our customers.
ECO QUALITY POLICY
Achieve Customer Satisfaction through
fulfilling applicable requirements and
continually improving metal finishing services.
ECO Quality Assurance starts at receipt of parts and orders. Incoming parts and documentation (POs, Prints, specifications, etc.) are reviewed to ensure parts are ready for processing, and all documentation is accurate. ECO processes are routinely tested and tracked. ECO utilizes a detailed part tracking system to monitor parts at every step through the process. When processing is complete, parts are tested and inspected to ensure applicable requirements are met.
ECO Quality Controls Include:
General:
- Incoming Parts and Documentation Inspection
- Chemical Bath Concentration Titrations and Spectrophotometric Analysis
- Copper Sulfate Passivation Testing
- Final Visual (magnified when applicable) Cosmetic Inspection
- DI and RO Water Use for Process-Critical Tanks
Specific to MEDCOAT and Electrolizing
– Thin Dense Chrome:
- Functional Testing includes:
- Thickness
- Adhesion
- Microhardness
- Embrittlement
- Porosity
- X-Ray Fluorescence Testing for Cr Thickness
Specific to Titanium Anodization:
- Color Verification to Standards
- Block and Ring Testing